An annual deck inspection ensures your deck is safe and sturdy. It’s a good idea to inspect decks for decay, damage, insects, and loose fasteners from the bottom up before tending to annual maintenance.
If you’ve recently built your deck or have had it for several years, it’s a good idea to schedule a professional inspection. Experienced contractors better understand the engineering of your deck and local building codes, so they can guarantee your deck is safe and identify any necessary repairs.
Explore this guide to deck inspections and download our checklist to evaluate your deck, and consult a local professional if you have any questions or concerns.
Download: Deck Inspection Checklist
Deck Inspection Tools
• Flashlight • Measuring tape • Level • Moisture meter | • Plumb bob • Hammer • Ladder • Screwdriver |
Substructure inspection
A deck’s substructure is often made of concrete footings, wood posts, and joists to create a supportive frame. It likely includes moisture resistance measures like flashing and water management systems, too.
Common substructure problems include:
- Weathering and moisture damage
- Wear and tear
- Ledger board separation
- Rusted or loose fasteners
- Wood rot
Deck substructures are almost always made of wood, so decomposition is a major concern to consider as you inspect your deck. Rotted wood feels soft and spongy, and may be dark or show cracks.
Check for wood rot by prying a chunk of wood away with a screwdriver or other probe. If it splinters, the wood is healthy. If the break splits in chunks without splinters, it may be rotted.
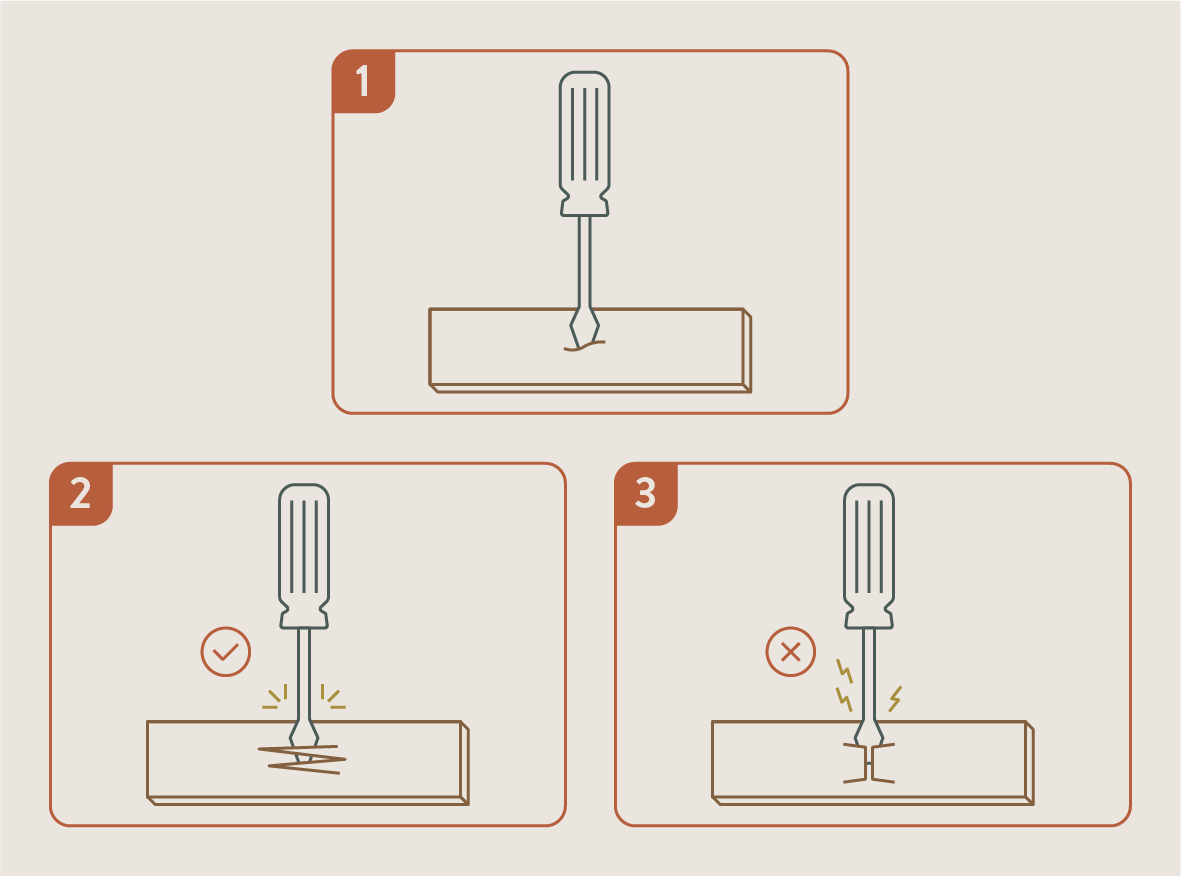
Footings and posts
Concrete footings help spread the load of a deck and its occupants over a greater surface foundation, and they connect to support posts to hold the full frame of a deck. This is the lowest part of a deck, so it’s a great place to begin your inspection.
Here’s what to look for while inspecting your footings and support posts:
- Proper water drainage
- Wood rot
- Insect infestations
- Warped or twisted wood
Joists and framing
The joists, rim boards, ledger boards, and blocking create a deck frame, which supports the deck’s surface, occupants, and furniture. Deck frames are typically wooden and vital to the safety and comfort of a deck, so it’s important to inspect for rot often.
Look for this damage while inspecting your deck’s frame:
- Wood rot
- Insects
- Sagging joists
- Secure outer rim joists
- Loose and damaged fasteners
- Gapping ledger boards
Ledger boards connecting a deck to a house’s foundation are especially important for the health and safety of your deck. If you spot debris buildup or gaps between the ledger and your house, remove any debris and tighten the lag screws to secure the board.
Flashing and water management
Flashing is a steel sheet installed over vital connections like the ledger board to prevent water and debris from reaching the wood. Flashing tape also prevents moisture damage and is easy to attach to wood joists.
Your deck may feature an under deck water management system like TimberTech’s DrySpace, which channels water away from the underside of an elevated deck to double your living space. If so, check that these systems flow currently and aren’t clogged.
These issues may contribute to moisture damage and need to be repaired:
- Water stains or rot around flashing
- Ledger board debris buildup
- Loose and damaged fasteners
- Proper water drainage
- Damaged flashing and flashing tape
Excessive moisture can lead to rot and mold issues. If you see green or fuzzy black mold and mildew spots on your deck, you can power wash the area and apply a fresh sealant to affected wood. Replace any heavily impacted boards.
Deck surface inspection
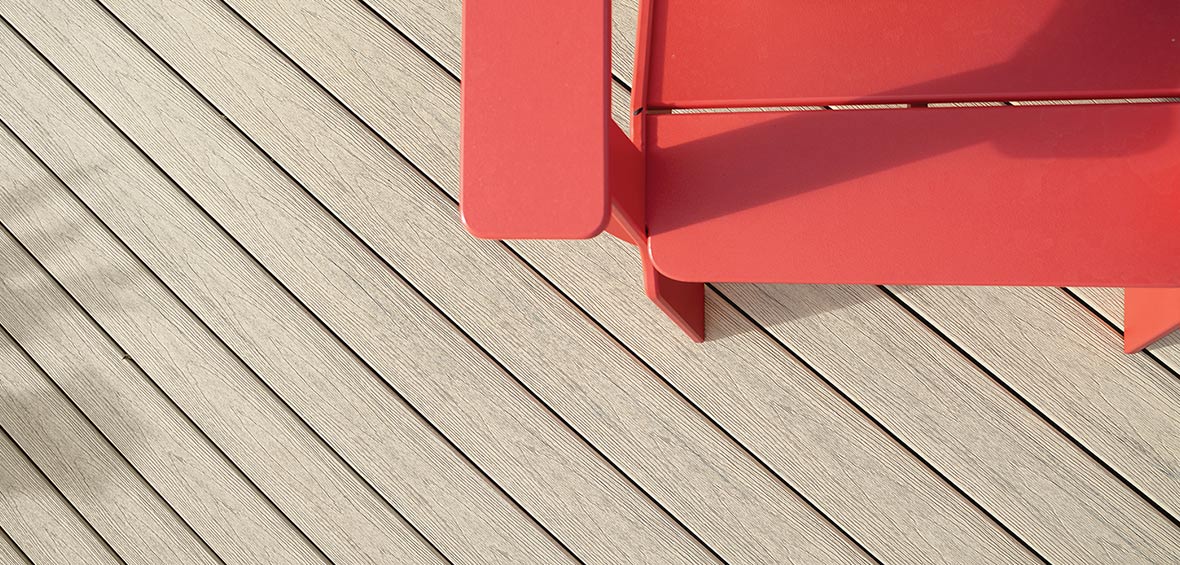
Homeowners are most familiar with their deck surface, including the decking boards, railing, stairs, and light fixtures. It’s easier to inspect these features and you may even be aware of a few problems, but an annual look over every spring is a great way to prevent accidents.
Common surface concerns include:
- Mold and mildew
- Cracked, splintered, or rotting wood
- Bowing or sagging deck boards
- Insect damage
- Loose railings
- Protruding fasteners
- Rusted or loose fasteners
Composite decking
Composite decking is made with a blend of wood fibers and synthetic polymers, and protected with polymer caps. These caps improve weather resistance and prevent mold, mildew, and fading, so composite deck damages and inspections aren’t nearly as extensive as wood decking.
It’s still important to evaluate and clean your composite decking annually by:
- Sweeping leaves, dirt, and debris
- Looking for loose or damaged fasteners
- Inspecting for bowing or sagging boards
Wood decking
Wood decking is highly susceptible to water damage and weathering. Splintering and cracks are inevitable, though you can improve your deck’s form and appearance with annual maintenance.
Wood deck owners should take some extra care to inspect for these concerns:
- Water damaged or rotting boards
- Insect damage
- Loose or protruding nails
- Wood in need of resealing
- Warped or bowed boards
Guardrails
Deck railing lines stairs and deck perimeters to increase stability and prevent falls. They’re not required for all decks — particularly those less than 30″ above grade — though this varies with local requirements.
Wood railings are susceptible to the same weather damage that wood decking and joists are, so you’ll need to look for rot. Homeowners with manufactured railing should still inspect their deck for secure attachments and damage.
- Inspect wood for splintering, rot, or insects
- Check for rusted, loose, or damaged screws and fasteners
- Look for loose, missing, or damaged balusters
- Ensure railing lights are working and properly installed
- Check that all railings are stable and don’t come loose with pressure
- Look for damaged or loose sections on the top and bottom rail
Test guardrails by pushing against them. A 180-pound person should feel secure placing their weight against the railing with little to no movement.
If the railing feels insecure, ensure that all fasteners are tight and in good condition. Cracked or improperly spaced balusters and rotted joists may also cause loose railings, so thoroughly inspect the structure from the top down.
Deck stairs
Stairs are the transition between your outdoor living space and backyard, and they may connect sections of a multi-level deck. They’re vulnerable to decay and shifting over time, which can become a hazard for your family and guests.
Ensure your deck steps are safe and inspect them for this damage:
- Wood decay
- Stair stringer breakage or rot
- Insecure attachments
- Warped or bowed steps and supports
- Loose or damaged treads
- Damaged or rusted fasteners
Professional deck inspection
While this is a great checklist for homeowners to evaluate the condition of their deck and make some minor repairs, a professional deck inspection guarantees that your structure is safe for your family.
Professional inspections are especially important if you have an elevated or multi-level deck that’s more complex than a simple platform deck. Structures exposed to salt water, direct sunlight, or boggy areas may also be more prone to rot or infestation and can benefit from a contractor’s experience.
Professional inspectors better understand the structural integrity and design of your deck, so they can evaluate nuances between wood species, appropriate deck loads, and proper attachments according to professional and local regulations. They can also recommend repair options or upgrades, like TimberTech’s Advanced PVC for waterside decks.
What happens if a deck fails inspection?
Professional inspectors frequently catch errors on DIY and professionally installed decks. It’s easy to overlook mistakes, and inspectors ensure that each structure is safe for use with a notice of necessary repairs. Consult the notice and your inspector to start corrections, and schedule another inspection once repairs are complete.
Whether you’ve just installed a brand-new surface or have enjoyed several summers on your deck, a proper deck inspection keeps your family safe and your deck looking great. Consult a contractor to discuss your deck’s condition and repairs.